Anabel recently moved offices, and her moving company made relocating a breeze.
However…she needs more furniture for her larger space.
The last time she ordered items and had them shipped, it was a disaster. Several items were left behind in the warehouse, and the ones she DID receive were damaged. It was a frustrating back-and-forth to even locate her items, and dealing with the warehouse was a nightmare..
Too bad she can’t trust the warehouse to be as thorough and careful as her moving company…
A moving company AND a storage distribution warehouse
While some moving companies only specialize in one facet of the receiving process, Appleton is proud to offer warehouse receiving and distributing, storage distribution, and delivery/installation services (our Final Mile service)
With Appleton, Anabel can partner with a warehouse to take care of her newly ordered furniture. We can connect the dots of the shipping process — bringing her items from point A (often an overseas manufacturer) to her office’s reception area.
Our warehouse is involved in receiving, inventorying, and delivering items.But what, specifically, is warehouse receiving?
What is warehouse receiving?
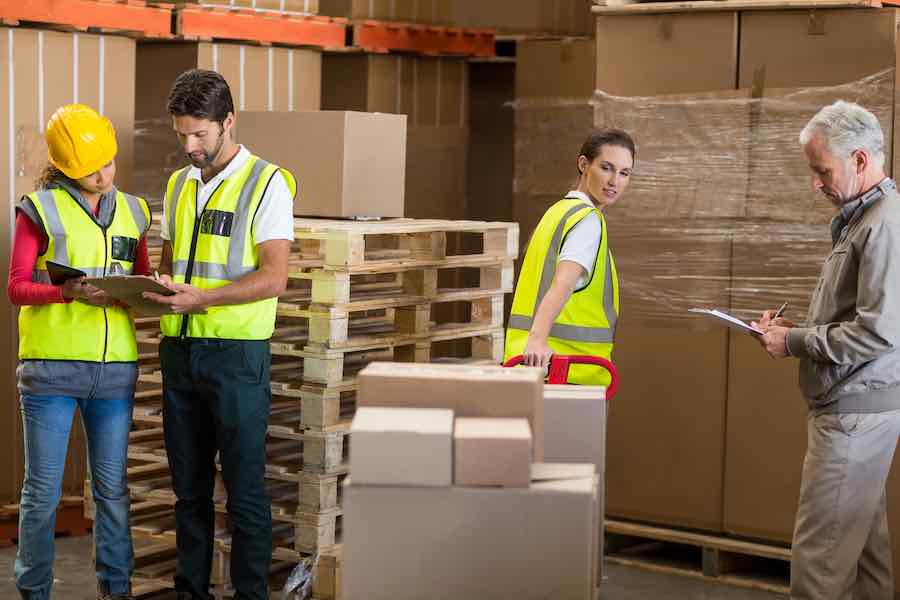
Over the past several years, there’s been a lot of talk about the supply chain — the process of getting goods from a manufacturer to a consumer. When it’s working well, a customer orders items, those items are shipped by a logistics company (a company that transports and coordinates the shipment of goods), and a warehouse receives them.
Warehouse receiving is this process of receiving, accepting, and inventorying goods so that they can be distributed.
The warehouse inventories the shipment, stores it and delivers the goods to a specified location — and ultimately products end up in the customer’s hands.
What is Appleton’s warehouse receiving process?
When we receive shipments into our warehouse, here’s how the process usually goes:
- A truck shows up with a shipment of goods with a bill of lading (the document required to move freight, which also acts as a receipt of the contents).
- We offload the shipment, and take note of any damages on the bill of lading so the driver has documentation.
- We accept the shipment, inventory the items, and house it in the warehouse until we get further directions from the logistics company.
What happens when we receive damaged items?
Sometimes, we receive items that have been damaged in transit.
Maybe something got broken, wet, or stained on its journey from the manufacturer to the warehouse.
When this happens, we coordinate with the logistics company to either refuse the damaged freight, dispose of it, or to send it to the customer with remediation.
How do we inventory items in the warehouse receiving process?
Appleton receives a huge variety of shipments — from furniture, to tissues, to pallets of diapers… just about anything!
Every article is meticulously inventoried as it was described in shipping. If the bill of lading lists 10 pallets of office paper — we inventory 10 pallets. If it’s listed as 5,000 boxes of work gloves — we count to make sure we’ve received 5,000 boxes into our inventory.
Although the shipment can contain any variety and number of goods, Appleton’s warehouse receives the information about the items and their scheduled arrival — and we manage that inventory on behalf of the customer. This service is called storage distribution.
What happens to items after the warehouse receiving process?
What happens to freight after warehouse receiving depends on the facility.
Some warehouses are “cross-dock” facilities that are a brief stop before distribution. Freight arrives at these terminal warehouses, then heads straight out for distribution.
Like we mentioned earlier, Appleton is a storage distribution warehouse. We not only receive shipments — we also provide the service of storing, managing, and shipping goods until the customer is ready for them.
Why would a company need a storage distribution warehouse?
Sometimes, a company doesn’t need all of the shipment delivered at once — and needs someplace to store them in the meantime.
Let’s take the company selling Anabel’s office couches, for example.
Maybe the distributor ordered 200 couches, but will need half delivered at the beginning of the month, and half at the end. Perhaps they had to order all 200 at once for pricing reasons or to fulfill an order minimum.
Whatever the reason that a company might need warehouse receiving and storage distribution, Appleton is here to take care of your shipment from the beginning of the process until the end!
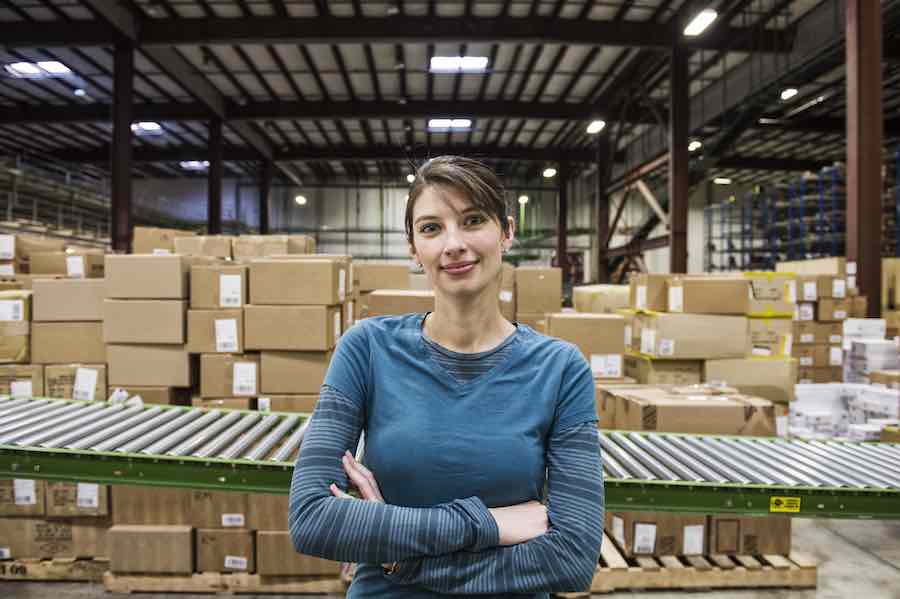
In the case of Anabel’s office couches, we can receive the shipment, inventory and manage the items, send them out on schedule — and even set them up in the office reception area for a seamless service!
Connecting the dots … from beginning to end!
At Appleton, we pride ourselves on meeting your storage and transportation needs — whatever they may be. With services in moving, storing, delivering, and installation, we’re able to partner with you to connect the dots between your shipment, customers, and you.
If you need a trusted partner for any part of the moving process, contact us today to find out how Appleton can help!